Why Are Paddle Dryers Essential for Precision Drying in Chemical and Pharmaceutical Industries?
Precision Drying Technology: How to Preserve Integrity and Bioactivity of Sensitive Materials in Pharma & Biotech Applications
3/27/20254 min read
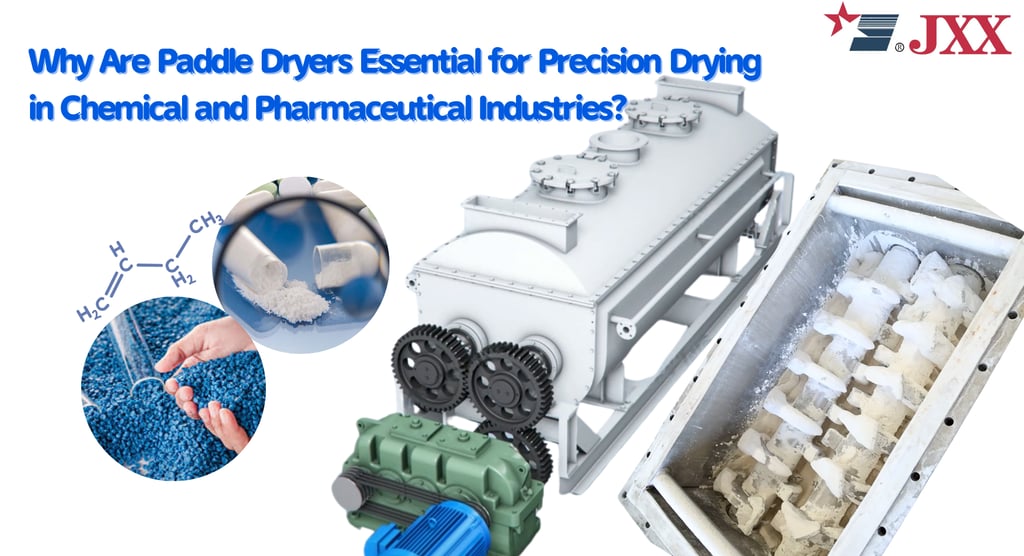
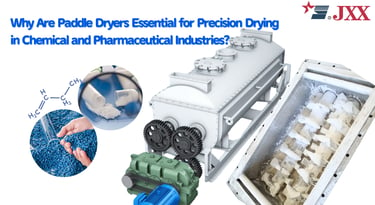
Paddle Dryer In the Chemical and Pharmaceutical Industries
In the chemical and pharmaceutical industries, precision drying of heat-sensitive materials—such as Active Pharmaceutical Ingredients (APIs), polymers, and specialty chemicals—is critical to ensuring product quality, regulatory compliance, and operational efficiency. As a cornerstone technology, paddle dryers excel in these sectors by enabling controlled low-temperature drying, high-efficiency solvent recovery, and contamination-free processes.
This article delves into the engineering principles behind paddle dryers, their design tailored for sensitive materials, and why they dominate applications demanding gentle thermal treatment and regulatory adherence.
Table of Contents
1
2
3
4
5
1. What Makes Paddle Dryers Ideal for Sensitive Material Drying?
Paddle dryers operate on indirect conduction heating, where materials are gently agitated by rotating paddles while heat transfers through hollow shafts and jackets. This method avoids direct contact with hot air, preventing thermal degradation of sensitive compounds like vitamins or polymers.
Vacuum variants (RVPDs) lower the boiling point of solvents, enabling efficient drying at temperatures as low as 30°C—crucial for preserving the bioactivity of APIs or heat-labile chemicals .
A 2023 study by Chemical Engineering Journal demonstrated that paddle dryers achieve 99.5% solvent recovery in pharmaceutical applications, outperforming spray dryers by 25% in energy efficiency. The closed-system design also minimizes cross-contamination risks, a key requirement for ISO 9001-certified facilities.
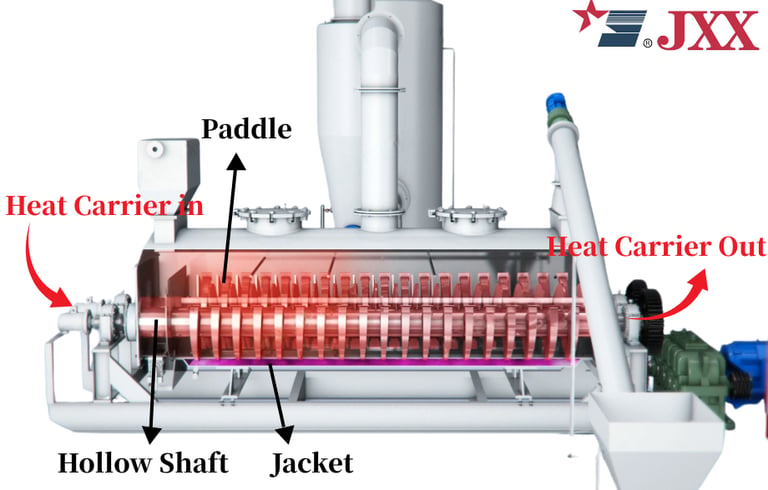
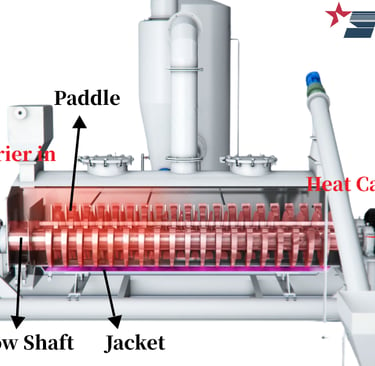
Core Advantages of JexDry Paddle Dryers
Indirect Heating Technology
Vacuum Environment for Lower Drying Temperatures
Uniform Mixing to Prevent Localized Overheating
Closed System Design for Contamination Control
2. How Do Vacuum Paddle Dryers Ensure Compliance with Pharma Standards?
Pharmaceutical-grade paddle dryers integrate vacuum systems, polished surfaces (Ra ≤ 0.8 µm), and CIP/SIP (Sterilization-in-Place) capabilities to meet strict FDA and EU Annex 1 guidelines. These features prevent microbial growth and residue buildup during API or excipient drying.
For example, drying hygroscopic materials like ascorbic acid requires precise pressure control (0.1–0.6 Torr) to maintain moisture levels below 0.5%, ensuring tablet stability and shelf life .
GMP-Compliant Critical Design Features of JexDry Paddle Dryer
Polished Surface (Ra ≤ 0.8 μm)
Dead-Corner-Free Design, Easy to Clean
Integrated CIP/SIP Systems
Validated Temperature/Pressure Control
A case study with a European pharma manufacturer showed that replacing a fluidized bed dryer with an RVPD reduced validation time by 40% due to easier cleaning and documentation of temperature/pressure profiles.
3. Can Paddle Dryers Reduce Energy Costs in Chemical Processing?
By recycling waste heat from exhaust gases and minimizing convective losses, paddle dryers cut energy consumption by up to 50% compared to conventional systems.
For instance, a Chinese chemical plant processing titanium dioxide slurry reduced annual energy costs by $320,000 after switching to a paddle dryer with heat recovery coils.
Energy Efficiency Advantages
Waste Heat Recovery System
Compact Design, Minimal Footprint
Precise Temperature Control, Reduced Overheating
Vacuum Operation, Lower Energy Consumption
Comparative performance of drying technologies in chemical applications
4. What Are the Critical Design Features for Hygienic Drying in Pharma?
Material Contact Surfaces: 316L stainless steel with electropolishing for corrosion resistance.
Sealing Systems: Double mechanical seals to prevent lubricant contamination.
Agitator Design: Paddles with breaker bars to eliminate material buildup in corners.
These features enable paddle dryers to meet 3-A Sanitary Standards and ASME BPE guidelines for biopharma applications.
Hygienic Design Advantages of JexDry Paddle Dryer
GMP & FDA ComplianceAgitator Design
Reduced Microbial Contamination Risk
Enhanced Product Quality & Safety
Simplified Cleaning Validation Process
5.Jexdry's Paddle Dryer Application in Polymer Processing (South Korea Client)
Client Background
Company: Sunchon Chemical Co., Ltd. (Location: Ulsan, South Korea)
Industry: Specialty Polymer Manufacturing
Material: Heat-Sensitive Polycarbonate (PC) Resins
Challenge
The client required precise drying of PC resins
(initial moisture: 35% → target: ≤0.5%) while avoiding thermal
degradation above 80°C. Traditional fluidized bed dryers caused
localized overheating (hot spots up to 95°C), resulting in 12% yield loss
due to polymer chain scission.
Jexdry's Solution
Deployed a Rotary Vacuum Paddle Dryer (RVPD) with:
Indirect Heating System
Hollow paddles and jacket circulated thermal oil at 65°C (±1°C precision), enabling gentle conduction heating (#).
Self-cleaning wedge-shaped blades eliminated material buildup, ensuring 98% heat transfer efficiency (#).
Vacuum Optimization
Operated at 0.5 Torr vacuum, reducing the boiling point of residual solvents (ethyl acetate) to 28°C (#).
Integrated solvent recovery system achieved 99.8% solvent reclamation (vs. 85% in rotary dryers) (#).
Hybrid Agitation
Dual-shaft paddles (10–15 RPM) provided axial plug-flow movement, reducing moisture variance to <1.2% across batches (#).
Breaker bars crushed agglomerates formed during the plastic phase (40–60°C) (#).
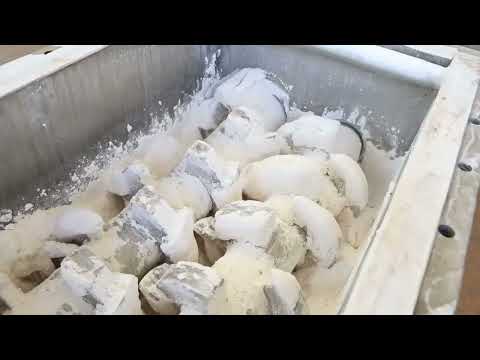
Conclusion
JexDry Paddle dryers are unmatched in delivering precision, compliance, and cost efficiency for chemical and pharmaceutical drying. By integrating vacuum technology, hygienic design, and energy recovery systems, they address the sector’s most pressing challenges—from solvent recovery to regulatory audits. For manufacturers prioritizing product quality and sustainability, investing in advanced paddle dryer technology is a strategic imperative.
External Links Recommendation:
[Case Study: Solvent Recovery in API Production]
Boost Your Drying Efficiency by 30% Talk to Our Engineers Now!
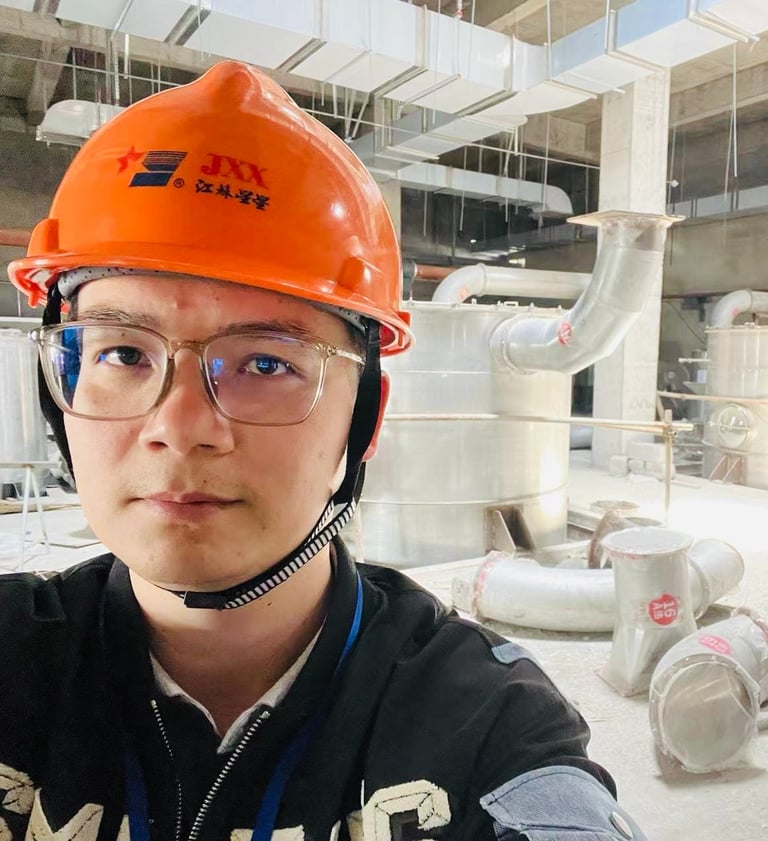
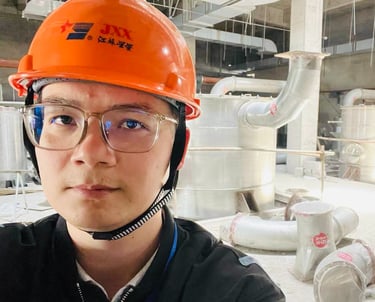
I’m Zar Zha, founder of jexdry.com, a trusted Chinese drying equipment manufacturer rooted in precision engineering since 1998.
As a family-owned business built on three generations of industrial innovation, we specialize in customized drying solutions for demanding industries like food processing, pharmaceuticals, and chemical production.
Over the past 25+ years, we’ve empowered 80+ countries and 200+ global clients—from Fortune 500 food giants to sustainable biofuel startups—to optimize their drying efficiency, reduce energy waste, and scale production safely.
At JexDry, we’re more than equipment suppliers; we’re partners in solving industrial drying challenges. I’m sharing decades of hands-on experience here to help engineers and plant managers master drying technology, avoid costly mistakes, and future-proof their operations.


Feel free to leave your information below, and we’ll get back to you as soon as possible. Alternatively, you can click the green WhatsApp button at the bottom of the page to contact us directly.
JexDry is a family-run business established in 1998, dedicated to providing customers with the most suitable drying equipment to make their production work more efficient, smooth, and environmentally friendly.
Products
Contact
+86-137-7501-3369
© 2024. All rights reserved.